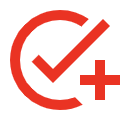
High capacity
Our facilities in Eupen, Hermalle-sous-Huy and Bierset are perfectly equipped to handle and store a wide variety of goods, including bulky or heavy items, increasing our capacity to cover all your logistics requirements.
How does our logistics solution work?
Our sites have diversified storage capacities, and each mission is monitored using our high-performance WMS (warehouse management system).
Our commitment is to ensure and optimise your logistics flows.
We have a logistics infrastructure at our sites in Bierset, Eupen and Hermalle-sous-Huy. Each site is designed to meet specific needs:
Our facilities in Eupen, Hermalle-sous-Huy and Bierset are perfectly equipped to handle and store a wide variety of goods, including bulky or heavy items, increasing our capacity to cover all your logistics requirements.
Our equipment is tailored to our many logistics services and includes: forklift trucks (front-loading or retracking), overhead travelling cranes up to 29 T, electric pallet trucks for order preparation, reinforced floors for reel storage, racks for pallet and length storage (cantilever), side or dock unloading, picking, (re)labelling, (re)packaging, sampling, destruction, cutting, etc.
Located close to major motorways, our sites ensure fast, efficient distribution throughout Europe. These strategic locations help to reduce transport times, improving our response to your logistics needs.
Thanks to our flexible storage capacities, including rack and block options, we can tailor space to the specific requirements of each product, giving you precise, personalised logistics management.
Do you have a question or need our logistics expertise?
If you have any questions about our services or would like to benefit from our know-how, contact Dennis Bebronne, our logistics expert. We are ready to help you and meet all your challenges. Trust Magetra Group to handle your freight logistics.
Contact our expertExpert in Logistics
Discover our FAQ
Below, you will find the answers to the questions most frequently asked by our logistics customers. Can’t find the answer to yours? Contact our expert now!
Would you like to consult our General Terms and Conditions for Logistics?
Our sites have all the necessary authorisations. We facilitate customs and excise management by working closely with partners who are experts in this field. This approach enables us to provide a complete, hassle-free solution for all your shipments falling under these regimes.
The stock is managed by a WMS (Warehouse Management System). This is software dedicated to stock and handling management. All goods passing through our 4 walls are identified and identifiable thanks to a unique barcode that can be read using a ‘gun’ reader. Stock can be managed according to FIFO (first in first out), LIFO (last in first out), best-before date or even batch number. To be sure that what is entered in the WMS is also physically on our premises, we offer our customers an annual inventory included in the storage price.
Invoicing is mainly based on 5 different rates. Administrative management of incoming and outgoing goods is invoiced per IN order and OUT order (an order is always linked to a transaction taking place on the same date and with the same origin, if IN, or the same destination, if OUT; in addition, it does not exceed the loading capacity of a vehicle). Goods handling is invoiced per handling unit (pallet, roll, reel, etc.) on entry (IN) and exit (OUT). Finally, the storage area itself is invoiced, which can vary depending on the nature of the storage (e.g. per m², per pallet, per kg, etc.). If you have any questions about your invoices, please do not hesitate to contact us.